Many companies wonder about the real payback of forklift training. One fact stands out: businesses with trained lift truck drivers see a 25% drop in accidents. This article will show you how investing in forklift education pays off, looking at cost vs. benefit.
Key Takeaways
- Forklift training lowers accidents by 25% and saves money on injury costs, which can be over $38,000 per incident. Trained workers also reduce insurance costs by 15% to 20%.
- Companies with trained forklift operators see a jump in productivity by up to 30%. This makes the workplace safer and faster.
- Following OSHA rules through proper training avoids fines and legal issues. It keeps companies safe from paying lots of money in penalties.
Understanding Forklift Training
Forklift training teaches people how to use lift trucks safely and efficiently. This training is not just important; it’s a must by law. It helps prevent accidents in places like warehouses and construction sites.
Training covers how to operate forklifts, understand safety rules, and handle materials without causing harm or damage.
Knowing how to run a forklift right keeps everyone safe. OSHA, the group that makes these rules, says this kind of education is key for any business that uses these machines.
Key Benefits of Forklift Training
Forklift training brings enhanced safety, improved productivity, and reduced operational costs to businesses. With this training, there are also lower insurance costs, enabling businesses to effectively manage their workforce and workplace safety more efficiently.
Enhanced Safety
Training workers to operate forklifts safely lowers workplace accidents. ITA research shows trained operators cause 25% fewer accidents. This training includes using safety gear and following clear rules while operating the heavy machines. NIOSH says 70% of forklift mishaps can be stopped with proper training.
With good teaching, employees learn how to avoid dangers. This cuts down on injuries linked to forklifts, which are often due to poor training. Every year, many get hurt from these accidents.
Making sure operators know how to handle these vehicles safely is key to keeping them and others safe at work.
Improved Productivity
Making work safer leads to making it faster too. Forklift training boosts how much a team can do in a day. Studies show certified operators are up to 30% more effective at their jobs. This means they move goods quickly and make fewer mistakes.
Investing in training doesn’t just help one worker; it lifts the whole business. A study by MHI found that businesses focusing on training saw a 15% jump in what they could do. It’s clear: learning how to use forklifts better pays off big for everyone involved, from the floor workers to the managers keeping an eye on the bottom line.
Reduced Operational Costs
Forklift training cuts down on costs in several ways. With proper training, workers handle materials more efficiently and safely. This leads to less damage to goods and equipment. Fewer accidents mean spending less money on repairs and replacements.
Also, well-trained forklift operators work faster, reducing the time it takes to move items around.
Training programs have another big benefit: they lower the risk of workplace injuries. The National Safety Council (NSC) found that a forklift-related injury can cost over $38,000.
A solid training program can cut these risks, saving companies lots of money on medical expenses and workers’ compensation claims. Plus, having such a program might reduce insurance costs by 15% to 20%, according to the Industrial Truck Association (ITA).
This makes forklift training a smart choice for businesses looking to save money and keep their workers safe.
Lower Insurance Costs
Decreasing operational costs directly reduces insurance premiums as well. Firms that implement forklift training programs notice a significant decrease in their insurance payments.
According to the ITA, such businesses can decrease their insurance expenses by 15% to 20%. This reduction is due to trained drivers causing fewer accidents, resulting in fewer claims for damages and injuries.
A safer workplace with fewer accidents is appealing to insurance companies. These firms often provide more favorable rates to businesses that actively work to minimize risks, such as by offering safety training.
By adhering to OSHA’s guidelines, companies can avoid hefty fines and simultaneously reduce their insurance bills. Thus, investing in forklift operator certification proves to be a financially wise choice in the long run.
Beyond Safety: The Financial Gains from Forklift Training

Forklift training goes beyond safety; it’s about reaping financial benefits. It leads to increased efficiency, reduced liability expenses, and boosts employee morale.
Increased Efficiency and Output
Training forklift operators makes them up to 30% more productive. This fact comes from the IWLA. With better skills, they handle materials faster and make fewer mistakes. They know how to use the machines in ways that speed up work but keep everything safe.
Businesses that invest in this training see a 15% rise in productivity, says an MHI study. This is because their workers can do more in less time. It’s not just about moving things around quicker. It also means less waiting for others to finish tasks, smoother workflows, and getting products out faster. Investing in operator training is investing in your business’s growth.
Reduced Claims and Liability Expenses
As businesses boost their forklift efficiency and output, they also cut down on workplace accidents. This leads to fewer compensation claims. Training plays a big role here. It can lower injury costs by 20% to 40%. This is because well-trained workers handle materials safely and use equipment correctly.
Following safety protocols prevents up to 70% of forklift mishaps, as found by NIOSH. Staying in line with OSHA standards helps too. It cuts down liability and insurance money spent. So, companies spend less on workers’ compensation and other related charges. This makes investing in employee training smart for lowering expenses linked to injuries at work.
Enhanced Employee Morale and Retention
Forklift training boosts worker happiness and keeps them on the job longer. A safe work environment makes employees feel valued and secure. This leads to less workplace stress and lower turnover rates. Happy workers are more likely to stay with a company, cutting down on costs linked to hiring new people.
Training also opens up more career chances for employees by giving them skills they can use in other jobs. This makes them feel good about their growth and ties to the company. Lower absenteeism rates follow as workers enjoy coming to their jobs, knowing they’re in a positive culture that looks out for their safety and growth.
Compliance and Legal Benefits
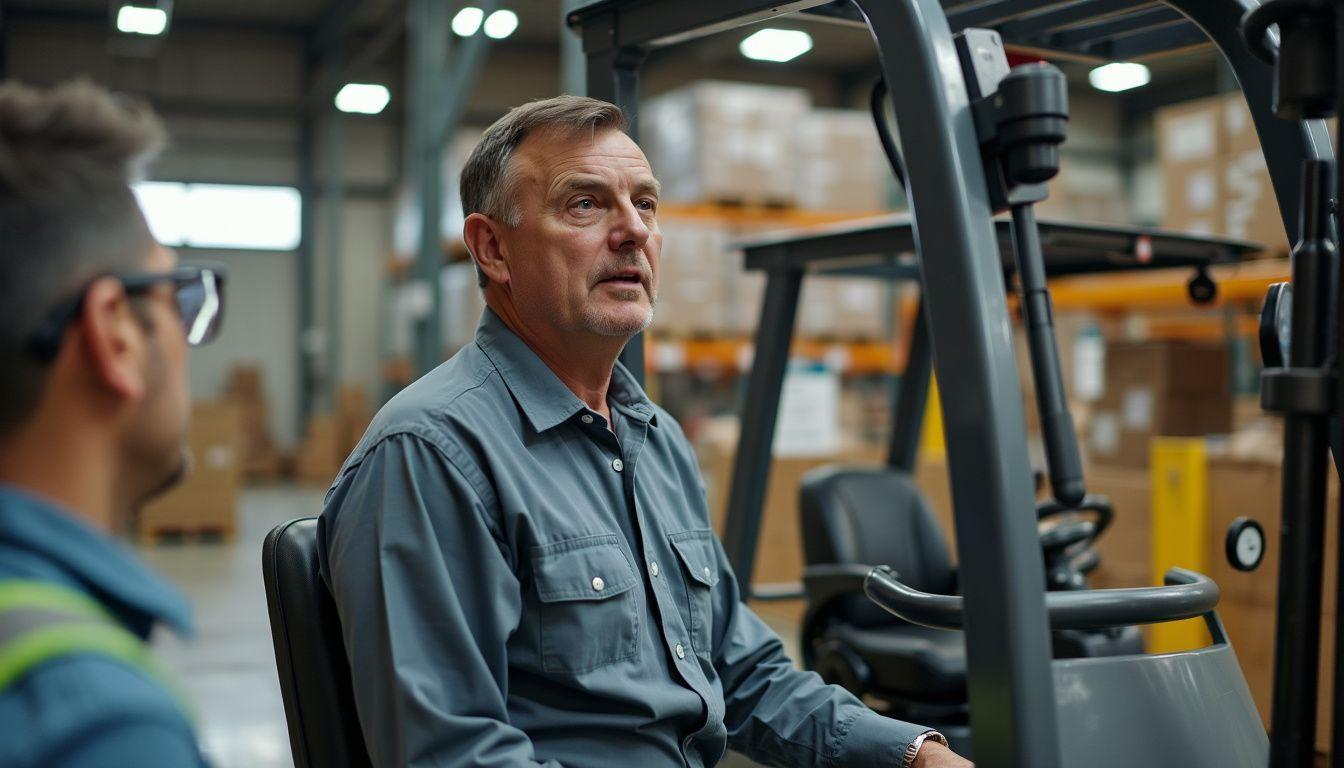
Ensuring Adherence to OSHA Regulations and Avoiding Legal Penalties through Forklift Training. Learn how compliance with occupational health and safety regulations can benefit your business in this section.
Adherence to OSHA Regulations
OSHA creates regulations for safe machinery operation. Specifically, Regulation 1910.178(l) requires employees receive proper training for safe forklift operation. Adherence to OSHA’s regulations aids companies in saving on worker injury costs, an expense that amounts to about $170 billion annually.
Compliance also results in decreased liability and insurance costs for businesses. OSHA compliance promotes a safer workplace while significantly lessening financial liabilities.
Companies gain substantial benefits through adherence to these safety regulations. It helps in avoiding hefty penalties and prevents worker injuries. Emphasizing safety results in less expenditure on accident-related costs and lowers insurance dues.
This commitment to health and safety enhances overall business operations, contributing to its long-term success.
Avoidance of Legal Penalties
Avoiding legal penalties is crucial for businesses. Non-compliance with safety regulations can result in fines or imprisonment. Moreover, compensation claims under the Compensation for Occupational Injuries and Diseases Act can be quite costly for businesses.
Ensuring proper forklift certification is mandatory not only guarantees safety but also ensures compliance with OSHA regulations, playing a significant role in avoiding expensive penalties.
The historical context underscores the importance of adhering to safety practices: since 1970, these measures have saved over 75,000 lives and prevented millions of injuries. By prioritizing adherence to these standards and ensuring that employees receive proper training and certifications such as forklift training benefits companies by preventing legal repercussions and hefty financial burdens associated with non-compliance.
Calculating the ROI of Forklift Training
To calculate the return on investment (ROI) of forklift training, consider the initial costs against long-term savings. Also, analyze its impact on business growth and brand reputation. This will help in understanding the financial benefits reaped from investing in forklift training.
Initial Costs vs. Long-term Savings
Understanding the balance between the initial investment and the long-term savings of forklift training is critical for businesses. The initial cost of forklift certification might seem like a big expense. Yet, it leads to significant savings over time.
Expense Type | Initial Costs | Long-term Savings |
Certification and Training | Cost of training programs and certification for employees. | Less money spent on fixing errors and lower injury rates. |
Injury Costs | High without training. | With training, businesses can save 20% to 40% on injury costs. |
Insurance Costs | Higher rates without employee certification. | 15% to 20% reduction in insurance premiums with a trained workforce. |
Productivity | Initial time investment in training. | Higher efficiency and output from well-trained employees. |
Compliance Penalties | Risk of fines without adherence to OSHA regulations. | Avoidance of legal penalties and compliance with laws. |
Training workers in forklift operation might cost upfront. But it saves money in many ways. For one, it cuts the average cost of an injury, which can be over $38,000. It also reduces insurance costs. Plus, it avoids fines by following OSHA rules. In short, investing in forklift training pays off by saving money and improving operations.
Impact on Business Growth and Brand Reputation
Forklift training positively influences business growth and brand reputation. A favorable workplace culture reduces costs and improves reputation, while certified operators boost productivity, driving business growth.
OSHA compliance reduces liability and insurance costs, directly impacting the bottom line. Employee morale and productivity are connected to a safer work environment.
This motivates businesses to invest in forklift training not just for efficiency but also for upholding a strong brand image in the industry. The financial benefits from forklift training extend beyond basic safety measures– they impact a company’s overall success by enhancing growth and consolidating its standing within the industry.
Strategies to Maximize ROI from Forklift Training
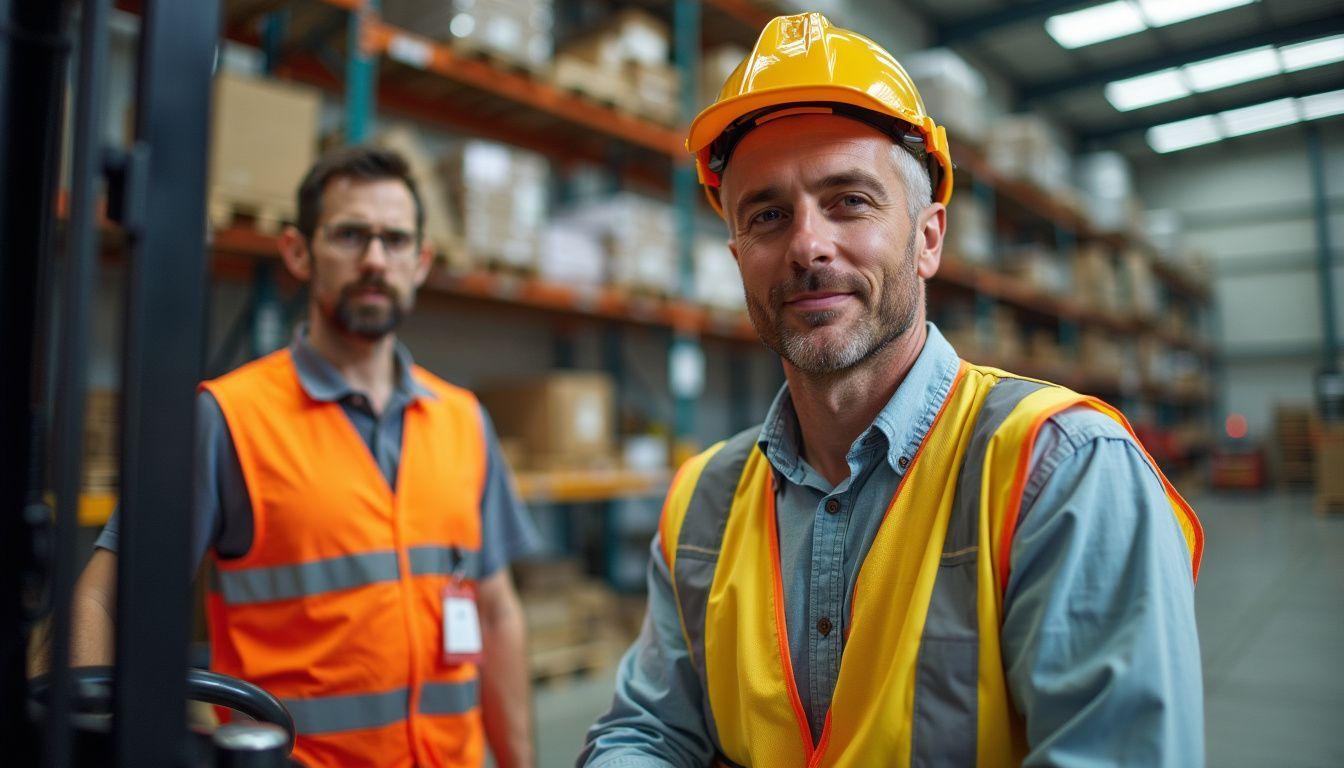
Maximize ROI by providing regular refresher courses for forklift operators. Invest in advanced training for complex operations to enhance safety and productivity.
Regular Refresher Courses
Regularly scheduled refresher courses are essential in keeping safety practices up-to-date and ensuring compliance with OSHA regulations. Here’s why they’re crucial:
- Fulfill Ongoing Training Needs: Throughout their careers, forklift operators need periodic refreshers to reinforce safe operating practices and stay current with new safety standards.
- Prevent Accidents: Refresher courses significantly decrease the risk of accidents, as 70% of forklift incidents can be prevented through proper training and adherence to safety protocols.
- Maintain Regulatory Compliance: These courses help companies adhere to OSHA regulations, avoiding penalties and legal liabilities.
- Boost Employee Morale: Regular training demonstrates a company’s commitment to employee safety, which in turn enhances morale and reduces turnover rates within the workforce.
- Keep Up With Best Practices: The dynamism of the industry demands continuous learning to incorporate new innovations and strategies that improve forklift operations.
- Enhance Skill Retention: Periodic training sessions help operators retain vital skills and knowledge necessary for efficient and safe forklift operations.
- Cultivate Safety Culture: By emphasizing regular training, employers foster a culture of safety consciousness that permeates the organization at all levels, reducing workplace accidents.
- Minimize Downtime: Well-trained employees lead to less downtime due to accidents or equipment damage, resulting in higher productivity and cost savings for businesses.
- Impact on ROI: Properly trained employees contribute positively to the overall return on investment (ROI) of the business by reducing operational costs related to accidents and downtime.
Advanced Training for Complex Operations
When it comes to enhancing workplace productivity and efficiency, advanced training for complex operations plays a crucial role. Here are some key aspects of this specialized training:
- Enhanced Handling Techniques: Advanced training equips forklift operators with specialized techniques to manage complex loads and operate in confined spaces.
- Risk Management Strategies: This training focuses on risk assessment and management, ensuring operators can tackle challenges effectively, reducing the possibility of accidents and damage.
- Optimal Equipment Utilization: Operators learn to maximize the capabilities of forklifts, ensuring efficient use of machinery during intricate tasks.
- Improved Problem-Solving Skills: Advanced training hones operators’ ability to troubleshoot technical challenges, leading to quicker issue resolution and minimized downtime.
- Adaptation to Technological Advancements: Training incorporates knowledge of cutting-edge technologies such as telematics systems and fleet management for improved operational control.
- Customized Operational Approaches: Tailored strategies are developed for specific operations, optimizing processes for greater efficiency and output.
- Safety Implementation: The training emphasizes integrating safety measures within complex operational tasks, prioritizing a secure working environment.
Conclusion
Investing in forklift training yields significant benefits for businesses. Certified operators not only improve workplace safety but also boost productivity and reduce operational costs.
This leads to improved compliance with regulations, decreased liabilities, and a higher return on investment. By prioritizing forklift training, businesses can ensure a safer and more efficient work environment while achieving long-term financial gains.