Forklift safety is crucial in any workplace using these powerful machines. We will discuss the top 10 forklift safety mistakes and provide practical tips to avoid them.
From not wearing seatbelts to improper parking, each mistake can lead to severe consequences. By following guidelines like wearing seatbelts and communicating with pedestrians, a safe working environment can be ensured.
Stay tuned to learn how to navigate forklift safety effortlessly!
Why is Forklift Safety Important?
Forklift safety is crucial to ensure workplace safety and compliance with regulations set by OSHA (Occupational Safety and Health Administration) to prevent accidents, protect pedestrians, and promote a secure working environment.
The Top 10 Forklift Safety Mistakes
Understanding the top 10 forklift safety mistakes is essential for preventing common mistakes that lead to forklift accidents and ensuring that operators are adequately trained and equipped with the necessary safety gear.
Not Wearing Seatbelts
Not wearing seatbelts is a critical safety mistake that can result in severe injuries or fatalities during forklift accidents.
Seatbelts are an essential safety feature designed to protect individuals in case of unforeseen circumstances. According to the National Highway Traffic Safety Administration, wearing a seatbelt can reduce the risk of fatal injury by up to 45% in passenger vehicles and up to 60% in light trucks. These statistics highlight the life-saving potential of this simple precaution.
In case of a sudden stop or collision, a seatbelt prevents occupants from being thrown out of their seats, thereby minimizing the impact of the crash. By securing themselves with a seatbelt, individuals can significantly increase their chances of survival and reduce the severity of injuries sustained during accidents.
Overloading the Forklift
Overloading the forklift beyond its load capacity compromises the stability of the forklift and increases the risk of accidents.
When a forklift is overloaded, it can lead to a variety of dangerous situations. The excessive weight can cause the forklift to tip over, especially when turning or on uneven surfaces. This not only puts the operator at risk but also jeopardizes the safety of those around the forklift. Overloading can result in structural damage to the forklift itself, leading to costly repairs and downtime.
To determine the load capacity of a forklift, one should refer to the manufacturer’s guidelines and load capacity plate on the machine. It is crucial to understand the limits of the forklift and never exceed them, even if it seems like a minor overload. Adhering to the load capacity ensures the safe operation of the forklift and reduces the likelihood of accidents in the workplace.
Improperly Parking the Forklift
Improperly parking the forklift can create obstacles and hazards for other workers and pedestrians, posing significant workplace safety risks.
Properly parking forklifts is crucial for a safe work environment. Clear communication about designated parking areas ensures that forklifts are parked in the right spots, reducing the potential for accidents. When forklifts are parked haphazardly, they can block emergency exits, obstruct pathways, and increase the risk of collisions.
One of the most common dangers of improper parking is the reduced visibility for other operators, leading to accidental collisions and damage to property. Implementing strict guidelines and regular training on parking procedures can help prevent these hazards.
Not Using Horns or Lights
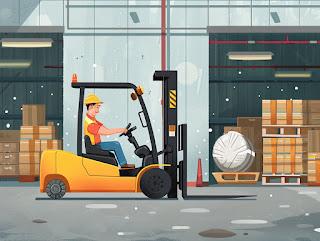
Failing to use horns or lights when operating a forklift can lead to collisions and accidents, especially in busy workplace conditions.
Using auditory and visual signals is crucial in any work setting to ensure effective communication and enhance overall safety. Clear and well-placed safety signage plays a significant role in guiding employees and visitors, promoting awareness, and preventing potential accidents. Visual cues such as bright colors, bold fonts, and universally understood symbols on safety signs can quickly convey important information, even from a distance. When combined with auditory warnings like horns, alarms, or spoken instructions, these signals create a comprehensive safety ecosystem that greatly reduces the risk of workplace incidents.
Not Checking for Obstacles
Not checking for obstacles before operating a forklift increases the likelihood of accidents and injuries in the workplace.
Regular inspections of the work area are crucial to ensure safety and prevent potential hazards. By taking the time to thoroughly check the surroundings, you can identify and eliminate any obstacles that could pose a risk while operating the forklift. One effective tip is to walk around the designated work area and look for any loose items, debris, or obstructions that could impede the smooth operation of the forklift.
Make sure to inspect the forklift itself for any issues that could compromise safety. Check the tires, brakes, lights, and controls to ensure they are all in proper working condition. This proactive approach helps create a safe environment for both the forklift operator and other workers in the vicinity.
Speeding or Reckless Driving
Speeding or reckless driving while operating a forklift significantly increases the risk of accidents and endangers both the operator and other workers.
Speeding not only reduces the operator’s reaction time but also compromises the stability of the forklift, leading to potential tip-overs and collisions. It is crucial for operators to adhere to designated speed limits within the workplace to ensure the safety of themselves and others.
Practicing safe driving habits such as maintaining a clear line of sight, avoiding sudden stops or sharp turns, and keeping a safe distance from obstacles can minimize the likelihood of accidents. By following these guidelines, forklift operators can create a safer working environment for everyone involved.
Not Following Proper Loading and Unloading Procedures
Not following proper loading and unloading procedures can result in load instability and accidents, jeopardizing forklift safety.
When preparing to load or unload materials, it is crucial to assess the weight and dimensions of the load to ensure it is within the forklift’s capacity limits. Inspecting the condition of pallets, containers, or other storage units is also essential to identify any damage that could compromise the stability of the load during transport.
Before lifting or lowering materials, it is important to secure the load with appropriate restraints or attachments, such as straps or clamps, to prevent shifting or falling off while in motion.
Using a Damaged or Malfunctioning Forklift
Using a damaged or malfunctioning forklift poses significant risks to workplace safety and increases the likelihood of accidents.
Regular inspections and maintenance are crucial to ensure the proper functioning of forklifts. By conducting routine checks on key components such as brakes, tires, hydraulic systems, and forks, operators can identify potential issues early on.
It is recommended to create a checklist for inspections to ensure thorough assessments. Any abnormalities or strange noises should be reported to supervisors immediately.
This proactive approach not only enhances safety but also prolongs the lifespan of the equipment, ultimately saving time and costs in the long run.
Not Communicating with Pedestrians
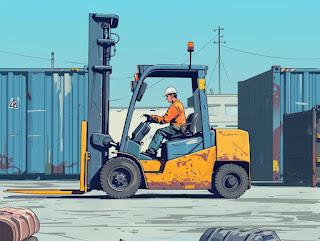
Failing to communicate with pedestrians in the work area can lead to accidents and injuries, compromising workplace safety.
Effective communication between forklift operators and pedestrians is crucial for maintaining a safe work environment. One strategy to enhance this communication is by implementing clear signage and designated walkways to indicate safe pedestrian paths. Regular safety training sessions for both forklift operators and pedestrians can help raise awareness of potential hazards and the importance of communication.
Encouraging a culture of mindfulness and awareness among all workers, emphasizing the need for eye contact and using clear hand signals, is also essential. Utilizing technology such as audible warning systems on forklifts can further improve communication and alert pedestrians of approaching vehicles.
Not Receiving Proper Training
Not receiving proper training and certification from accredited institutions like Forklift Academy can result in unsafe practices and non-compliance with OSHA regulations.
Comprehensive training and certification are crucial elements in ensuring workplace safety and regulatory compliance. By equipping individuals with the necessary knowledge and skills, organizations can mitigate risks, prevent accidents, and maintain a productive work environment.
Forklift Academy plays a vital role in this process by offering top-notch training programs that cover all aspects of forklift operation, maintenance, and safety protocols. Their experienced instructors provide hands-on guidance to students, helping them understand best practices and avoid common pitfalls. With certification from Forklift Academy, individuals can demonstrate their proficiency and commitment to workplace safety, enhancing their employability and contributing to a culture of compliance.
How to Avoid These Mistakes
By following best practices and receiving proper training, you can avoid common forklift safety mistakes and significantly reduce the risk of injuries and accidents in the workplace.
Wear Seatbelts at All Times
Wearing seatbelts at all times while operating a forklift is a simple yet effective measure to prevent serious injuries during accidents.
Seatbelts serve as a crucial safety feature, acting as the first line of defense in case of sudden stops, collisions, or tip-overs. In case of an impact, they distribute the force of the crash across the stronger parts of the body, reducing the risk of severe injuries.
Real-life stories abound with instances where wearing seatbelts have made a life-saving difference. From preventing individuals from being ejected during rollovers to keeping them securely in place during abrupt halts, these restraints are a testament to their effectiveness.
Ensuring that all operators consistently adhere to wearing seatbelts is vital. Employers can implement regular safety training sessions, conduct spot checks, or even have seatbelt usage incorporated into daily checklists to instill a culture of safety within the workplace.
Know the Weight Capacity of Your Forklift
Knowing the weight capacity of your forklift is essential for maintaining stability and preventing accidents caused by overloading.
One of the key aspects to consider when determining the load capacity of a forklift is to check the manufacturer’s specifications and guidelines provided in the operator’s manual. These documents will outline the maximum weight the forklift can safely carry without compromising its stability.
Ignoring these load capacity limits can lead to a range of serious consequences, including tipping over, loss of control, or even structural damage to the forklift. Exceeding load limits can also result in safety hazards for the operator, other workers, and potential damage to the goods being transported.
Park the Forklift in Designated Areas
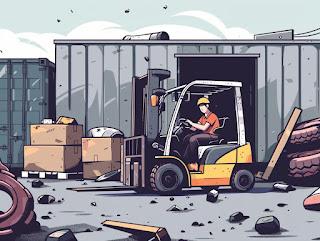
Parking the forklift in designated areas helps to avoid creating obstacles and hazards for other workers and pedestrians.
By following proper parking protocols, businesses can maintain a smooth workflow within their facilities. Designated parking areas are strategically placed to ensure the efficient movement of materials and goods. When operators park forklifts in these specified zones, they contribute to overall workplace safety and organization.
To park a forklift safely, it’s crucial to consider factors such as positioning, visibility, and stability. Positioning the forklift in a way that does not block walkways or emergency exits is essential. Always engage the parking brake and turn off the ignition before exiting the vehicle.
Use Horns and Lights to Alert Others
Using horns and lights to alert others in the workplace is crucial for preventing collisions and ensuring safety in various workplace conditions.
Auditory and visual signals serve as essential communication tools to navigate busy work environments. Auditory signals, like horns, are particularly useful in areas with limited visibility or when machinery is in operation.
For instance, when operating a forklift in a warehouse, using the horn before turning around corners helps avoid unexpected collisions with pedestrians. On the other hand, visual signals, such as flashing lights, can indicate potential hazards or alert others of ongoing maintenance work.
Proper utilization of these signals not only enhances safety but also fosters a culture of awareness and caution among workers.
Check for Obstacles Before Moving
Checking for obstacles before moving the forklift is vital to avoid accidents and ensure a safe working environment.
Creating a checklist for inspecting the work area is a crucial step in maintaining safety standards. This checklist should include scanning for loose objects, debris, spills, or any potential hazards that could impede the forklift’s path.
Regular inspections not only demonstrate a commitment to safety but also help identify and address issues proactively. By staying vigilant and conducting thorough checks before each operation, workers can significantly reduce the risk of accidents and injuries.
Follow Speed Limits and Drive Safely
Following speed limits and driving safely are fundamental practices for minimizing the risk of accidents and ensuring forklift safety in various workplace conditions.
Adhering to speed limits not only prevents collisions but also allows operators to have better control over the forklift, reducing the likelihood of tipping over or losing stability. It is crucial to maintain a safe distance from obstacles, pedestrians, and other vehicles in the work area to avoid potential accidents.
Safe driving practices involve keeping a clear line of sight, avoiding sharp turns and sudden stops, and using the horn or signals when necessary to communicate with others in the vicinity. Regularly inspecting the forklift for any maintenance issues and ensuring that the load is properly secured before operation are also essential steps for safe driving.
Properly Load and Unload Materials
Properly loading and unloading materials is critical for maintaining stability and preventing accidents during forklift operation.
When loading materials onto a forklift, it is essential to distribute the weight evenly and place the heaviest items on the bottom for balance. Securing the load with straps or chains is crucial to prevent shifting during transport. Regular inspections of the forklift, as well as the materials being transported, should be conducted to identify any potential hazards or issues that may compromise safety. Prioritizing these procedures ensures a safe working environment for both the operator and those in the vicinity.
Report Any Issues with Forklift to Supervisors
Reporting any issues with the forklift to supervisors promptly is essential for maintaining workplace safety and preventing potential accidents.
Regular inspections of the forklift can help identify any potential problems early on, reducing the risk of breakdowns or malfunctions during operation. By promptly reporting issues, you not only contribute to a safer work environment but also ensure that necessary maintenance tasks are carried out in a timely manner.
To effectively communicate with supervisors about forklift concerns, be clear and specific when detailing the problem. Providing details such as the nature of the issue, when it was first noticed, and any relevant observations can help the maintenance team address the problem efficiently.
Remember, proactive communication and collaboration with your supervisors are key in ensuring that forklift safety protocols are adhered to and potential hazards are mitigated before they escalate.
Communicate with Pedestrians and Other Operators
Communicating with pedestrians and other operators is crucial for preventing accidents and ensuring a safe working environment.
It is essential to establish clear protocols for communication, such as using hand signals or radio systems to coordinate movements and tasks. Effective communication can help avoid misunderstandings that may lead to collisions or other hazards.
For example, in a warehouse setting, a forklift driver should signal when they are reversing to alert pedestrians in the area. Such simple yet effective communication practices can significantly reduce the risk of accidents and improve overall safety in the workplace.
Receive Proper Training and Certification from Forklift Academy
Receiving proper training and certification from accredited institutions like Forklift Academy is essential for ensuring safe forklift operation and compliance with OSHA regulations.
Comprehensive training programs play a crucial role in equipping forklift operators with the knowledge and skills necessary to handle these powerful machines safely. Certification from Forklift Academy not only validates an individual’s competency but also demonstrates a commitment to workplace safety and regulatory compliance.
Employers benefit from having certified forklift operators as it reduces the risk of accidents, injuries, and costly fines due to non-compliance. A workforce trained by Forklift Academy helps to create a culture of safety awareness and responsibility within the organization.