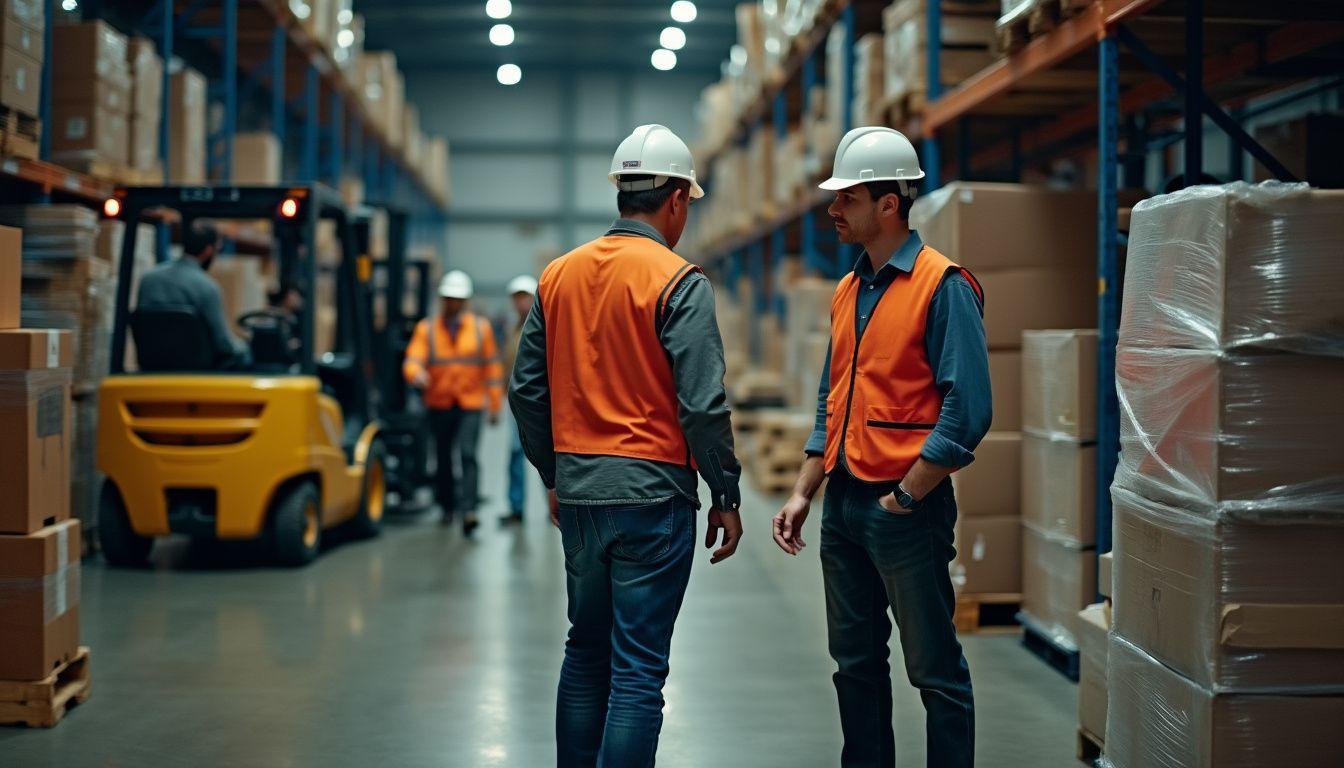
Worried about OSHA inspections for your forklift operations? You’re not alone. Forklift safety is crucial to pass these checks. Our guide offers practical steps to prepare for OSHA inspections.
Key Takeaways
- OSHA checks forklift safety at work. They want only trained people to operate forklifts.
- Daily checks on forklifts are a must. This includes looking at brakes, leaks, and safety gear like seat belts.
- Fix any broken parts before using the forklift again. Records of all fixes should be kept up to date.
- Training is key to keep workers safe around forklifts. It covers how to drive, handle loads, and what to do in emergencies.
- Testing emergency plans helps prepare everyone. Practices include fire drills and learning how to use fire extinguishers correctly.
Understanding OSHA Inspections for Forklift Safety
OSHA inspections cover safety regulations for forklifts. Compliance with OSHA standards is crucial for workplace safety.
What Do OSHA Inspections Cover?
OSHA inspections make sure forklifts are safe at work. They check if only trained operators use the forklifts, as required by law (29 CFR 1910.178(l)). Inspectors look at daily checks before using the forklift.
If a forklift runs all day, it must be checked after every shift (29 CFR 1910.178(q)(7)). They also review how well the workplace follows safety rules.
The inspections cover more than just checking if the seat belt works or if there are leaks. They go deep into seeing if emergency procedures and material handling rules are in place and followed correctly.
Inspectors test different parts like brakes, exhaust systems, and fluid levels too. They want to see that everything works right to keep workers safe from harm.
Importance of Compliance
Maintaining OSHA standards is essential for safeguarding employees around forklifts. Non-adherence to these standards can result in substantial issues, such as penalties and possible criminal charges for employers.
Annually, incidents involving powered industrial trucks lead to expenses of $135 million for companies. To bypass these costs and legal complications, employers need to adhere to the protocols defined by OSHA for training to operate these vehicles safely.
Disregarding OSHA’s PIT standard not only endangers lives but also subject businesses to significant financial penalties.
By adhering to 29 CFR 1910.178(l), employers ensure their teams are well-versed in proper forklift handling. This isn’t merely to avoid penalties; it’s to avert incidents that could potentially harm individuals or even result in fatalities.
With the National Emphasis Program (NEP) focusing on warehouses and distribution facilities in 2023, abiding by OSHA’s priorities is crucial for keeping your workspace both safe and efficient.
Preparing Your Warehouse for an OSHA Inspection
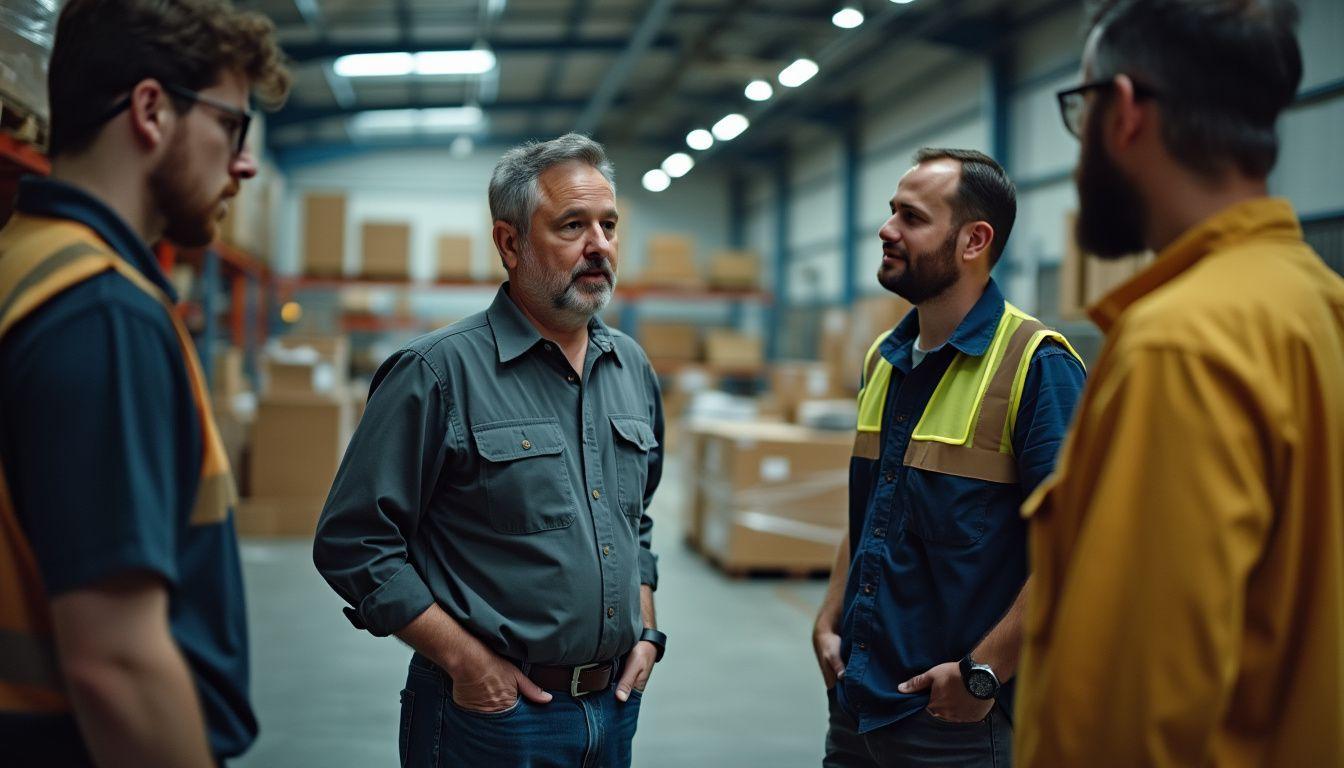
When preparing your warehouse for an OSHA inspection, start by conducting a self-assessment. Review material handling procedures to ensure compliance with safety standards. Test emergency procedures to make sure they’re effective in real situations.
Conduct a Self-Assessment
To get ready for an OSHA inspection, a self-assessment of your warehouse is key. This helps spot and fix safety issues early.
- Check all forklift trucks daily before use. Look for leaks, damage, or worn parts that need fixing.
- Make sure the parking brake works well every time. It’s crucial to stop the forklift when needed.
- Inspect propane tanks on gas-powered forklifts for any signs of damage or leaks.
- Verify the levels of engine oil and hydraulic fluid are full to prevent breakdowns during operation.
- Review operators’ familiarity with the operator manual and ensure they follow it closely.
- Test safety devices like seat belts and overload alarms to see they function right.
- Look over the forklift’s lifting gear, including hoist and lowering control, to ensure smooth operation without hazards.
- Examine safety training records to confirm all workers have current knowledge on operating forklifts safely.
- Assess emergency procedures to make sure everyone knows what to do in case of an accident.
This list sets a solid foundation for passing an OSHA inspection by focusing on key areas that affect warehouse safety and health. Next, we’ll dig into material handling procedures and how they play into preparation for OSHA checks
Review Material Handling Procedures
Material handling procedures are key to keeping workers safe and ensuring compliance with the Occupational Safety and Health Administration (OSHA). These rules help manage how goods move around, using equipment like forklifts.
- Make a list of all equipment used for moving materials. This includes pallet trucks and internal combustion engine vehicles.
- Check that each piece of equipment has up-to-date maintenance records. Look for reports on hydraulic hoses, brake pedals, and transmission fluid levels.
- Train every worker on how to use the equipment safely. Make sure they know about pre-start visual checks and how to control the vehicle.
- Set up regular safety meetings to talk about proper ways to load and unload goods, especially at loading docks.
- Make emergency plans clear to everyone. Workers should know what to do in case of fire or a spill.
- Use signs to mark areas where only trained operators can go with machinery.
- Keep aisles clear to avoid accidents with forklifts moving around.
- Install mirrors at corners to help drivers see other people or machines coming.
- Make sure there’s enough light in areas where workers move materials.
- Post guidelines near each piece of equipment, showing steps for safe operation.
Next, let’s focus on ensuring forklift safety standards are met in the workspace.
Ensure Forklift Safety Standards are Met
Making sure forklifts meet safety standards is key. This involves regular checks and fixing problems fast.
- Perform daily operational checks on all forklifts. Look at things like drive control and tilt control to see they work right.
- Follow OSHA rules, which say you must check forklifts every day before use. If a forklift runs all the time, inspect it after each shift.
- Take out any forklift that is broken or not safe from service right away. Tell someone about the issue without delay.
- Keep a record of all maintenance and repairs done on each forklift. Use this to show OSHA inspectors that you are up to date.
- Test how well your workers can use personal protective equipment (PPE). Make sure they know when and how to use it.
- Review emergency plans often with your team. Make sure everyone knows what to do in case of fire or gas leaks from LP gas-powered forklifts.
- Train your staff well using online courses or learning management systems about safety rules and driving forklifts safely.
- Set up smart systems that remind you when it’s time for preventative maintenance to avoid breakdowns or harmful emissions from the vehicles.
- Use tools like augmented reality (AR) simulators for safer training without real risks.
- Always have Material Safety Data Sheets (MSDS) easy to find in case of spills or exposure to harmful substances during operations.
Following these steps helps keep everyone safe and your warehouse running smoothly while meeting OSHA requirements.
Test Emergency Procedures
After making sure your forklifts meet all safety standards, it’s time to test emergency procedures. This step is key to OSHA compliance and worker safety. Here are ways to do just that:
- Run fire drills regularly. This helps everyone know how to leave the building quickly and safely if there’s a fire.
- Check alarm systems often. Make sure fire alarms and smoke detectors work well.
- Practice using fire extinguishers. Workers should know where they are and how to use them.
- Review evacuation routes with all employees. Everyone should know the best way out no matter where they are in the warehouse.
- Test emergency stop buttons on forklifts. They must work right away when needed.
- Do mock rescues for trapped drivers after a tip-over accident, simulating real-life situations without risk.
- Ensure clear signals for emergency communications are in place, such as loudspeakers or two-way radios.
- Confirm that all exits are not blocked and clearly marked, making sure paths are wide enough for quick escapes.
- Prepare a contact list of all key personnel like firefighters, paramedics, and police to call during emergencies.
- Conduct surprise inspections to make sure employees follow safety rules every day.
- Keep first aid kits full and easy to find in several places around the work area.
Testing these procedures makes your workplace safer for everyone by preparing them for real emergencies.
The Ultimate Forklift Safety Checklist
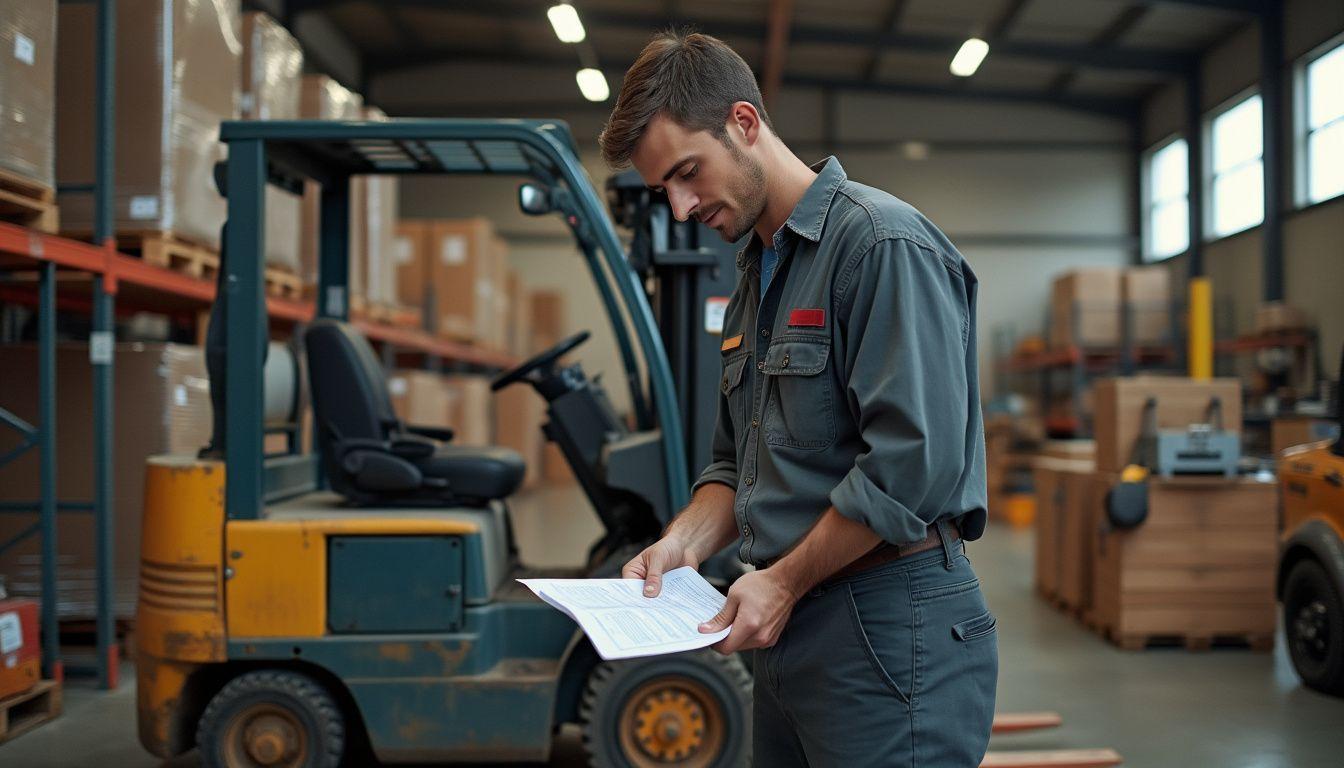
Ensure the forklift undergoes daily operational checks and that all maintenance and repairs are well-documented. Find out more about keeping your forklifts safe.
Daily Operational Checks
Daily operational checks are key for forklift safety. They help spot problems before they lead to accidents. Here’s a list of what to check every day:
- Check the accelerator linkage. Make sure it moves smoothly without sticking.
- Test the brakes. They should stop the forklift quickly and evenly.
- Look at the steering. It must respond well without any delay.
- Examine drive control. It should shift without any issues.
- Inspect tilt control. The forks should tilt forward and backward correctly.
- Review hoist/lowering control. Lifting and lowering actions must be smooth.
- Press the horn. It needs to be loud enough to warn people nearby.
- Turn on lights and alarms if your forklift has them, to ensure they work right.
Doing these checks can prevent accidents in your warehouse or construction site, keeping workers safe under OSHA guidelines for health and safety inspection standards.
Maintenance and Repairs Documentation
After checking your forklifts every day, you need to keep track of any fixes or upkeep. This step is key for safety and OSHA rules. Keep a log for each forklift. In it, write down all the maintenance work and repairs you do. Also note when you find something wrong with a machine.
OSHA says that if a forklift has problems, don’t use it until it’s fixed. The rule (29 CFR 1910.178) tells us exactly when to take a truck out of service and how to report issues. Use logs to show that you follow these guidelines.
Good documentation keeps everyone on the same page and proves compliance.
The Importance of Forklift Training to Ensure Safety
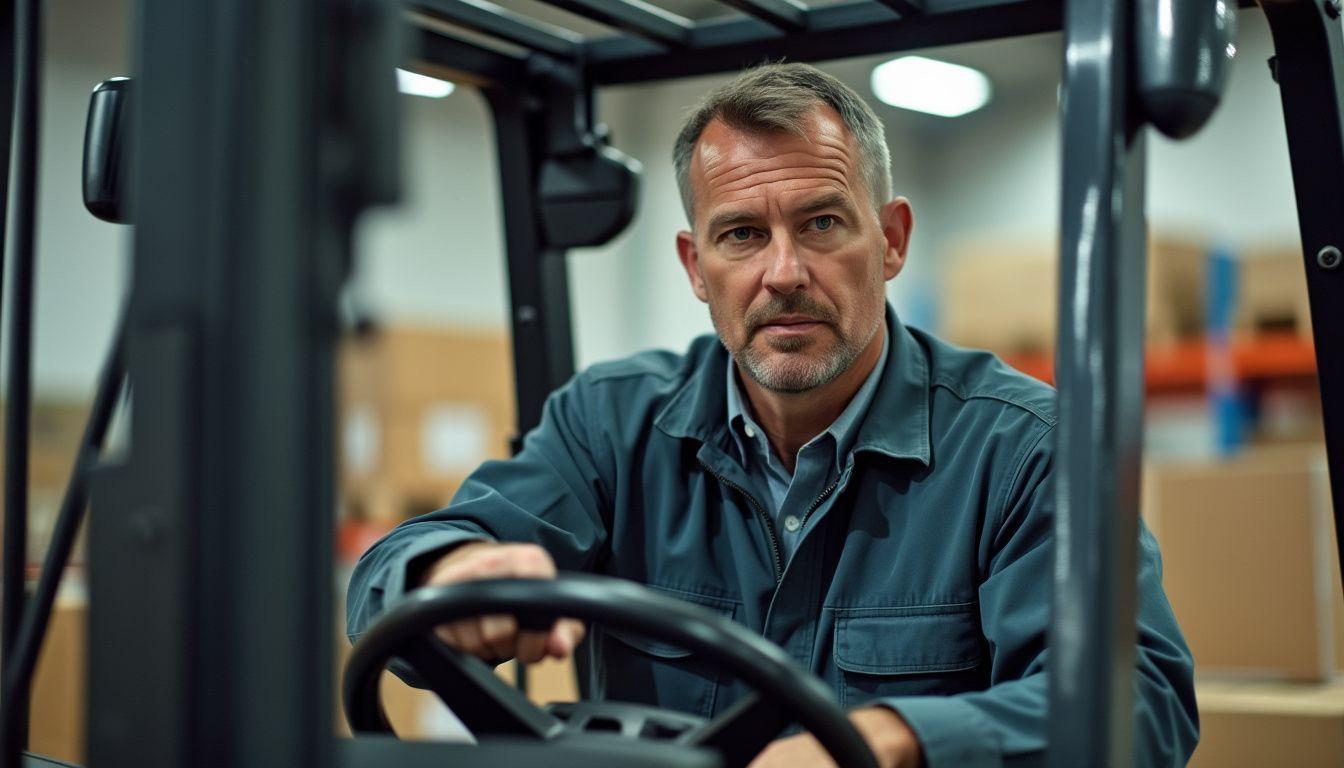
Forklift training keeps everyone safe at work. OSHA rules say workers must learn and show they can run a forklift safely. This keeps accidents low. Training covers driving, lifting loads, and what to do in an emergency.
It makes sure drivers know how to handle the truck right.
Forklift Academy offers courses that meet OSHA’s requirements for powered industrial truck training. They ensure that individuals are fully prepared to operate forklifts safely. Workers gain hands-on experience through tasks that closely mirror their daily job responsibilities. With this comprehensive training, workplaces become safer for everyone working around forklifts.
Conclusion
In conclusion, preparing for OSHA inspections for forklift safety is crucial to ensure workplace compliance and protect workers. Daily operational checks and proper maintenance are essential to meet OSHA standards.
Employers must prioritize forklift training to reduce accidents that lead to serious injuries and fatalities annually. It’s important to take proactive measures in ensuring forklift safety in the warehouse.
The HVI APP can be utilized as an effective tool for conducting thorough inspections, contributing to a safer work environment.
FAQs
1. What is OSHA and why does it matter for forklift safety?
OSHA, or Occupational Safety and Health Administration, sets standards to protect workers from hazards like flames during operation and maintenance of equipment such as forklifts. It’s important to adhere to these rules not just for safety but also because they conduct safety inspections.
2. How can I prepare my company’s forklifts for an OSHA inspection?
Preparation involves regular preventive maintenance and predictive maintenance of your vehicles. This includes checking the three-point hitch system on your machines regularly, ensuring all parts are in good working order.
3. Can technology aid in preparing a warehouse facility for an OSHA inspection?
Yes, tools like smartphones can assist with asset management by automating routine checks which helps improve overall safety conditions before any official vehicle inspection takes place.
4. What protections do employees have if they report unsafe conditions?
Employees who report hazardous situations enjoy whistleblower protections under federal law, ensuring their rights if they raise concerns about workplace safety including issues related to anti-money laundering efforts.
5. Who else besides OSHA should be concerned about fire risks at a warehouse using heavy machinery like Forklifts?
The local Fire Marshall often plays a role in inspecting facilities that use heavy machinery due to the potential risk of sparks or flames causing fires.