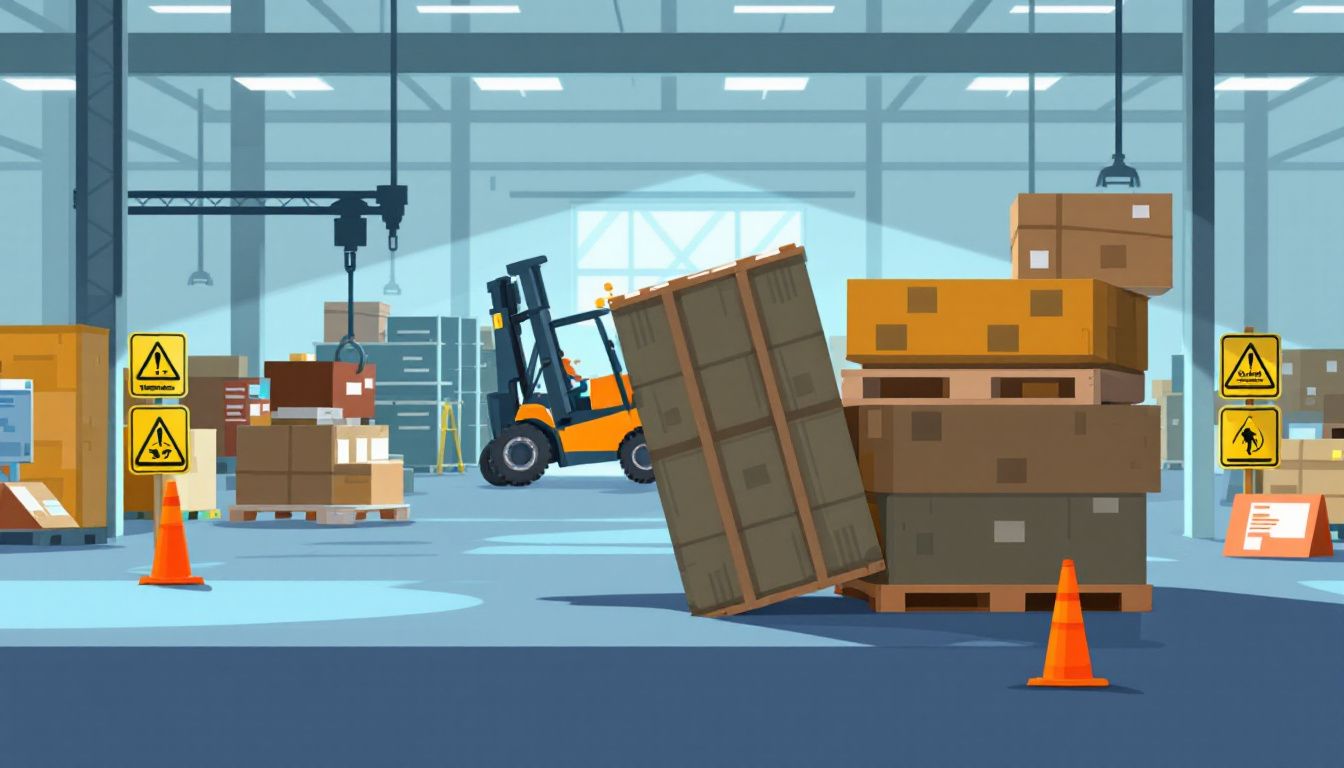
Forklifts are super useful, but, boy, can they be dangerous! Dropping a load on your foot isn’t exactly a picnic, and nobody wants that. Sadly, forklift hazards can cause real problems, sometimes even deaths, for workers.
The National Institute for Occupational Safety and Health (NIOSH) tracks these accidents and offers safety tips. This post covers the top five forklift hazards you absolutely must avoid.
Want to stay safe? Read on.
Key Takeaways
- Blind spots are a major hazard, so operators should drive in reverse when visibility is limited.Training, like that offered by Forklift Academy, can help operators handle blind spots safely.
- Unsecured and loose loads can cause accidents and damage.Proper training on securing loads and understanding weight limits is crucial.
- Improper operation, like speeding and sharp turns, is dangerous.OSHA-certified training promotes safe forklift operation.
- Poor maintenance can lead to accidents.Regular checks of fluids, tires, brakes, forks, and safety features are essential.Keep maintenance records.
- Pedestrians are at risk in forklift areas. Clear signage, safe walking zones, and pedestrian awareness are important for preventing accidents.OSHA (Occupational Safety and Health Administration) provides guidelines (29 CFR 1910.178) for forklift safety, including training requirements.
Blind Spots
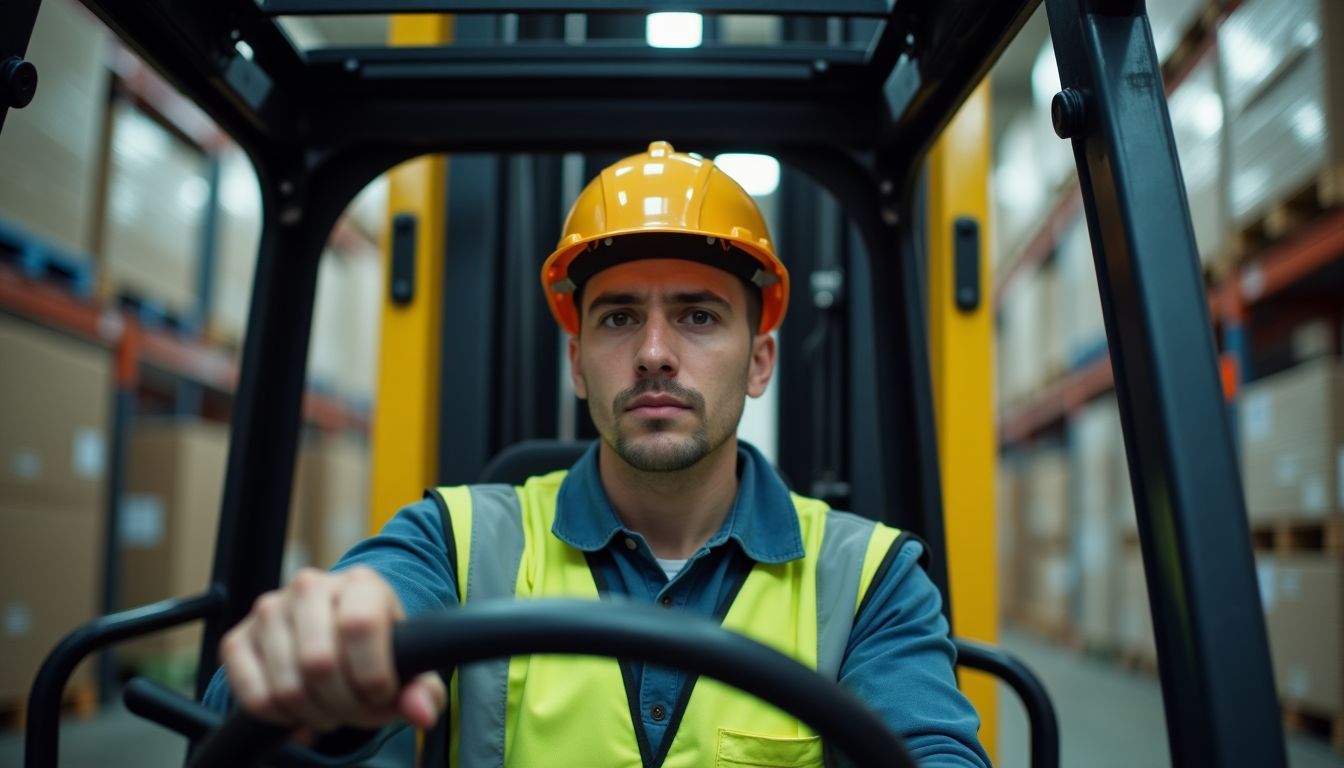
Large loads can block an operator’s view. This makes seeing pedestrians and other obstacles difficult. Blind spots are a serious threat. They are one of the top twelve forklift hazards in warehouses.
Think of it like trying to parallel park a van with no back windows. Not fun, right? If you can’t see, drive in reverse. This improves visibility. Limit traffic in busy areas. Educate pedestrians about forklift safety.
This helps everyone stay safe. Enroll in Forklift Academy for online forklift training. Get your OSHA Forklift Certification.
Good training from an online program like Forklift Academy can help prevent accidents. It teaches operators how to handle blind spots.
Unsecured Loads
Loose loads are a recipe for disaster. Imagine a Jenga tower tipping over. That’s what an unsecured load on a forklift can do. Falling objects cause injuries. They damage products.
They create chaos. Loose loads are one of the top 12 forklift hazards in warehouses. Train your team. They need to know how to secure loads. They must understand weight limits. This keeps everyone safe.
Let’s move on to how these powerful machines are handled.
Improper Operation and Use
Forklift cowboys, listen up! Speeding and sharp turns are a recipe for disaster. Think of your forklift like a shopping cart loaded with eggs – a sudden stop or turn, and you’ve got a scrambled mess.
OSHA-certified training can prevent these boneheaded moves. Don’t be a statistic. Get trained. Operate safely.
Poor Maintenance Practices
A busted forklift is a dangerous forklift. Ignoring upkeep can lead to disaster, so check out more info on good maintenance habits.
The Ultimate Guide to Forklift Maintenance
Forklifts need regular TLC. A well-maintained forklift is a safe forklift.
- Check fluids daily. This includes oil, water, and hydraulic fluid.Low levels can cause big problems.
- Inspect tires for wear and tear. Look for cuts, bulges, or anything unusual.Flat tires are no fun.
- Test the brakes. Make sure they’re working properly.You need to stop on a dime.
- Examine the forks.Look for cracks, bends, or other damage. Damaged forks can drop loads.
- Check safety features. Lights, horns, and seatbelts are vital.These keep you safe.
- Clean the forklift.Remove any debris or buildup. A clean machine runs better.
- Keep records of all maintenance.This helps track any issues.Good records are important.
Pedestrians also face risks around forklifts. Let’s talk about those next.
Pedestrian Hazards
People walking near forklifts are like bowling pins waiting for a strike. Distracted pedestrians don’t always see the big machines coming. This creates a dangerous mix. Mark safe walking zones with bright tape.
Put up clear signs. These simple steps can prevent accidents. Pedestrians in forklift areas are a major safety concern. They must stay aware.
How to Mitigate Forklift Hazards
Want to keep your warehouse a safe and productive zone? Check out these simple strategies to minimize forklift risks.
Proper Training for Operators
Training is key for safe forklift operation.OSHA guidelines stress training and certification, especially for young workers.
- Certified forklift training prevents accidents.It stops injuries and serious problems.OSHA certification addresses improper use issues.
- Training covers safe handling procedures.It includes load capacity limits and stability principles.Operators learn pre-shift inspections.
- OSHA emphasizes hands-on training.This builds practical skills and safe practices.It includes supervised driving experience.
- Training addresses specific job site hazards.It covers pedestrian traffic and confined spaces.It teaches proper communication methods.
- Refresher training is crucial.It reinforces safety procedures and addresses new regulations.It helps maintain operator proficiency.
Good training creates a safer work environment. Let’s discuss regular equipment maintenance.
-What Does OSHA Stand for in Forklift Training
OSHA means Occupational Safety and Health Administration. It’s part of the U.S. Department of Labor. They’re like the workplace safety police. They offer lots of helpful stuff. Think safety rules, help following those rules, and training.
Forklift safety is a big deal for them. They even have special rules just for forklifts. You can find these in 29 CFR 1910.178. This section covers powered industrial trucks. It’s their way of keeping forklift operators safe.
OSHA wants everyone to go home in one piece.
OSHA’s forklift training isn’t just about acronyms. It’s about real-world safety. It covers everything. This includes inspections, safe driving, and load handling. A good training program follows OSHA’s guidelines.
This keeps both workers and the company out of trouble.
Regular Equipment Maintenance
Keeping your forklift in tip-top shape is key. Regular maintenance keeps your team safe and productive.
- Check it out: Inspect your forklift before each use. Look for anything broken or unsafe. Don’t use a damaged forklift. Report problems right away.
- Stick to the schedule: Regular maintenance is vital.It keeps forklifts safe.Follow the manufacturer’s recommendations. Create a consistent maintenance schedule.
- Don’t skip maintenance:Insufficient maintenance is a common hazard. It can lead to accidents. It’s crucial for safety.
What Must Be Done Daily Before Using a Forklift
Daily checks keep your forklift humming and you safe.A quick look-over can prevent big problems.
- Check the tires: Look for cuts, bulges, or low pressure.Flat tires can cause tip-overs. Nobody wants that.
- Inspect the forks:Look for cracks, bends, or other damage. Damaged forks can drop loads.That’s a safety hazard.
- Test the brakes: Make sure they work well.Bad brakes are a recipe for disaster.
- Check fluids:Look at oil, water, and hydraulic fluid levels. Low fluids can damage the forklift.
- Inspect safety devices:Test the horn, lights, and seatbelt. These are important for your safety so don’t skip them.
- Look for leaks: Check for oil, water, or fuel leaks. Leaks can cause fires or slips.
- Examine the mast:Look for damage or wear. A damaged mast can collapse.Avoid unsafe equipment.
- Check the steering: Make sure it’s responsive.Bad steering can cause accidents.
- Inspect the controls: Make sure they work correctly. Faulty controls are dangerous.
- Conduct inspections before use: This is the golden rule.A quick check can save you big headaches.
Implementation of Safety Protocols
Daily checks keep forklifts running smoothly.Safety protocols take it a step further.
- Hazard Assessments: Employers must assess risks before forklifts enter new areas. Think of it like scouting out a new hiking trail. You want to know what you’re getting into.
- Traffic Management: Create a traffic plan.This plan should include pedestrian-safe zones. It’s like planning routes in a busy city.
- Safe Zones: Mark safe zones clearly.Use safety tape and signs.Make them really obvious. Nobody wants a forklift sneaking up on them.
- Signage: Use clear signs.These signs warn of forklift traffic.Think big, bold, and easy to understand.
- Training: Train all operators properly.This training should cover safe operation.It also includes understanding the hazards.
Conclusion
So, let’s wrap this up. Forklift safety isn’t just a good idea, it’s crucial. Ignoring these hazards can lead to big trouble, like injuries or worse. Keep your team safe and your business running smoothly by taking forklift safety seriously.
Prioritize training and maintenance—it’s worth it.