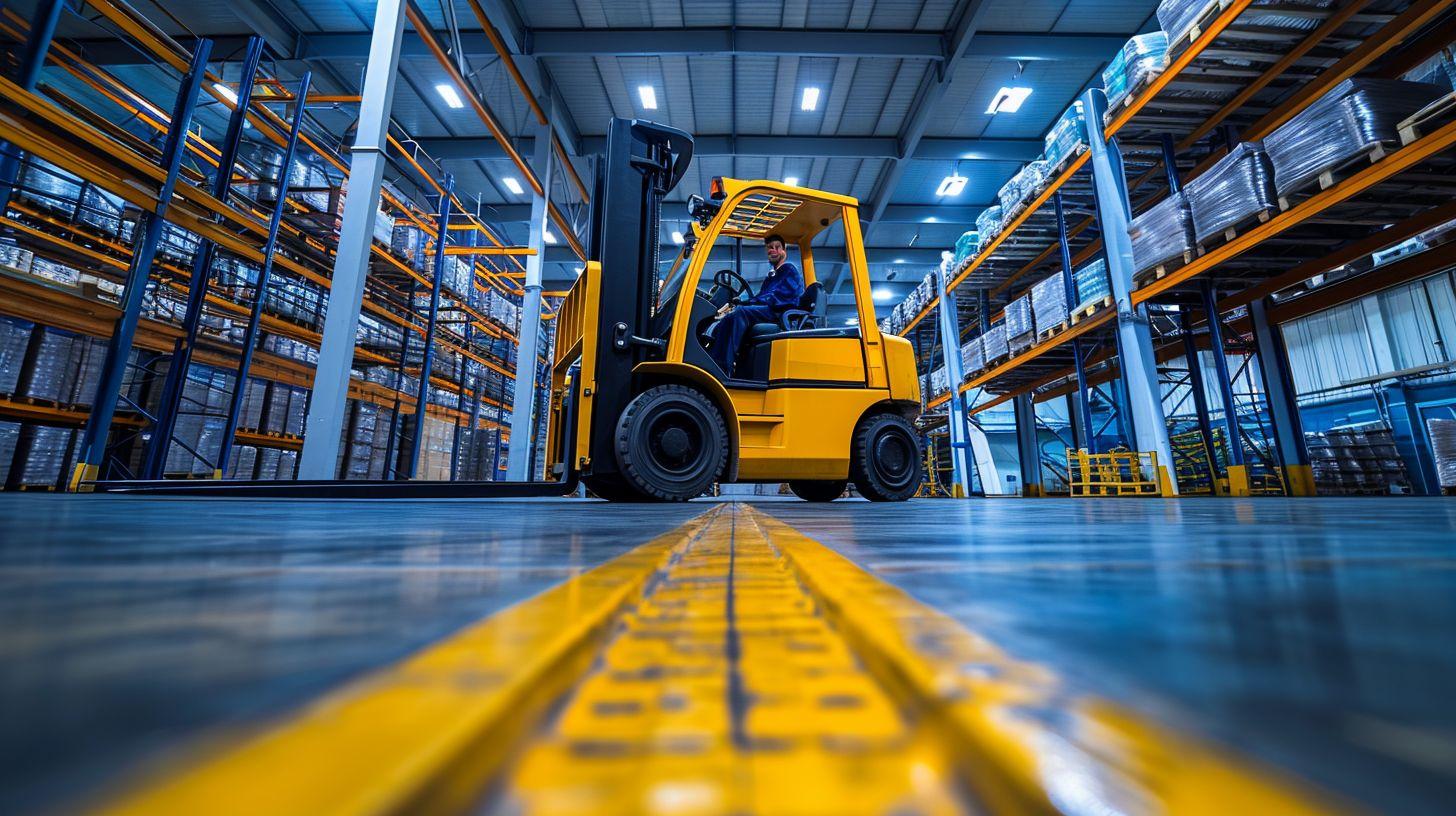
Before powering up a forklift, there’s an essential routine to keep everyone safe. Did you know that OSHA insists on daily safety checks before operating any forklift? Our blog walks through the crucial steps to ensure your lift is ready and secure, safeguarding you and your team.
Keep reading; it’s all about staying safe out there!
Key Takeaways
- Every day, forklift operators must conduct safety checks before using the equipment to avoid accidents and maintain efficiency. This includes both visual pre-operation inspections and operational inspections.
- Specific checklists should be used that include examining fluid levels, brakes, steering, lights, alarms, and seatbelts to ensure everything functions properly according to OSHA guidelines.
- Different types of forklifts such as electric, internal combustion, and liquid propane have unique inspection requirements which must be carefully followed to ensure safe operation.
- Regular maintenance checks at 250 – hour intervals can catch minor issues before they become serious problems. More extensive checks should be performed every 500 hours and major maintenance is needed after 2,000 hours of operation.
- Cleanliness is vital not just for the machine’s longevity but also for safety; keeping a clean workspace helps identify hazards while operating a forklift.
Importance of Conducting Forklift Safety Checks
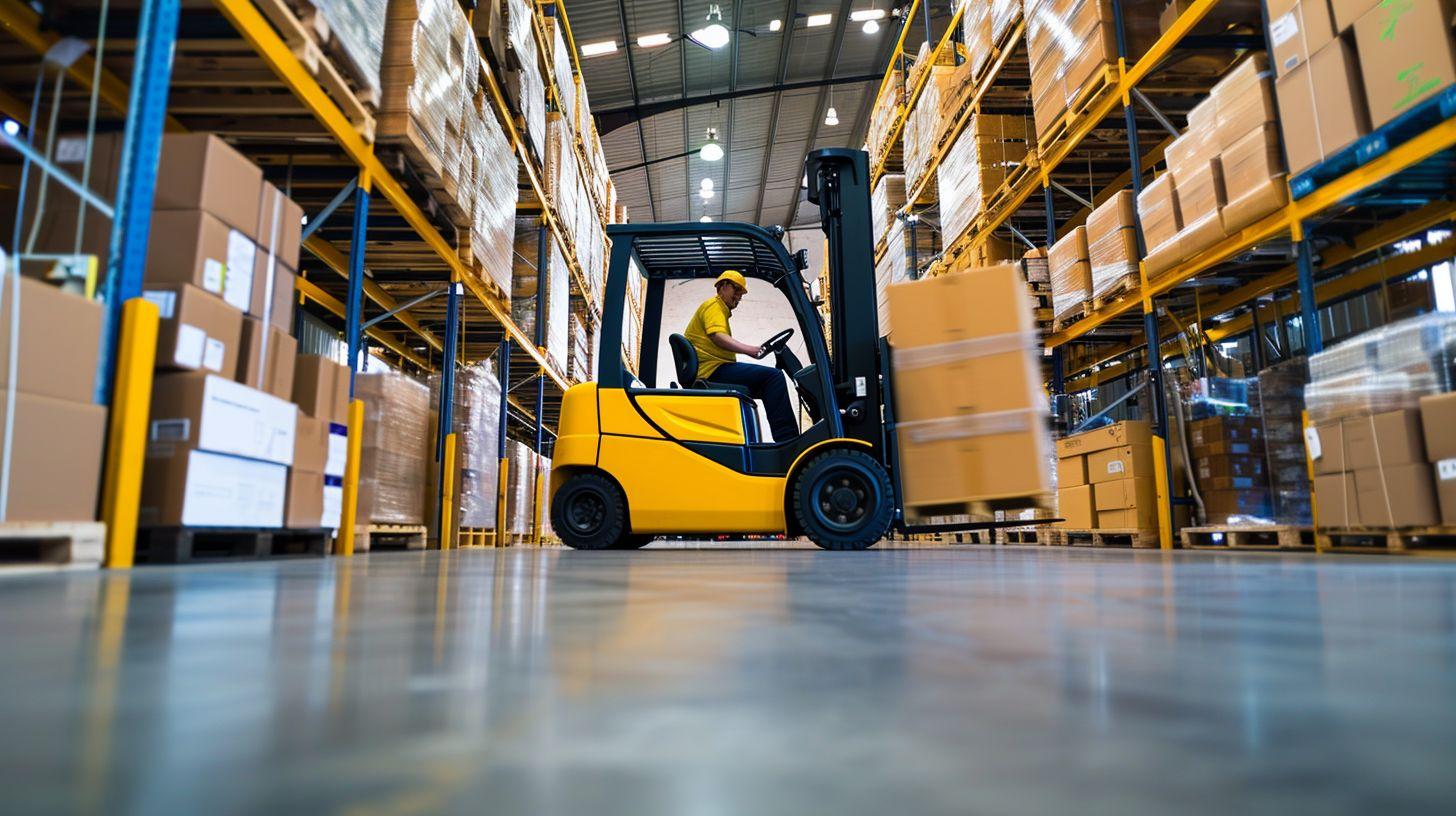
Conducting forklift safety checks before each shift can prevent accidents and save lives. Forklifts are heavy, powerful machines that pose serious risks if not properly maintained or operated.
Safety inspections uncover potential mechanical problems like faulty brakes, leaks in the hydraulic hoses, or damaged fork condition which could lead to equipment failure or accidents during operation.
Checking fluid levels and ensuring that forklift attachments are secure also minimizes the risk of malfunction.
Ensuring a forklift is in top working condition enhances workplace efficiency since regular maintenance reduces unexpected breakdowns and downtime. It’s crucial to ensure all safety decals and nameplates are legible and that limit switches function correctly to keep both the operator and surrounding employees safe from harm.
After completing safety checks, operators have peace of mind knowing their vehicle meets occupational safety standards set forth by agencies such as OSHA, reducing the likelihood of legal action due to non-compliance-related incidents.
Following thorough inspections, we move on to understanding how exactly these critical daily assessments are performed through an operational inspection checklist.
How to Conduct a Daily Forklift Safety Inspection
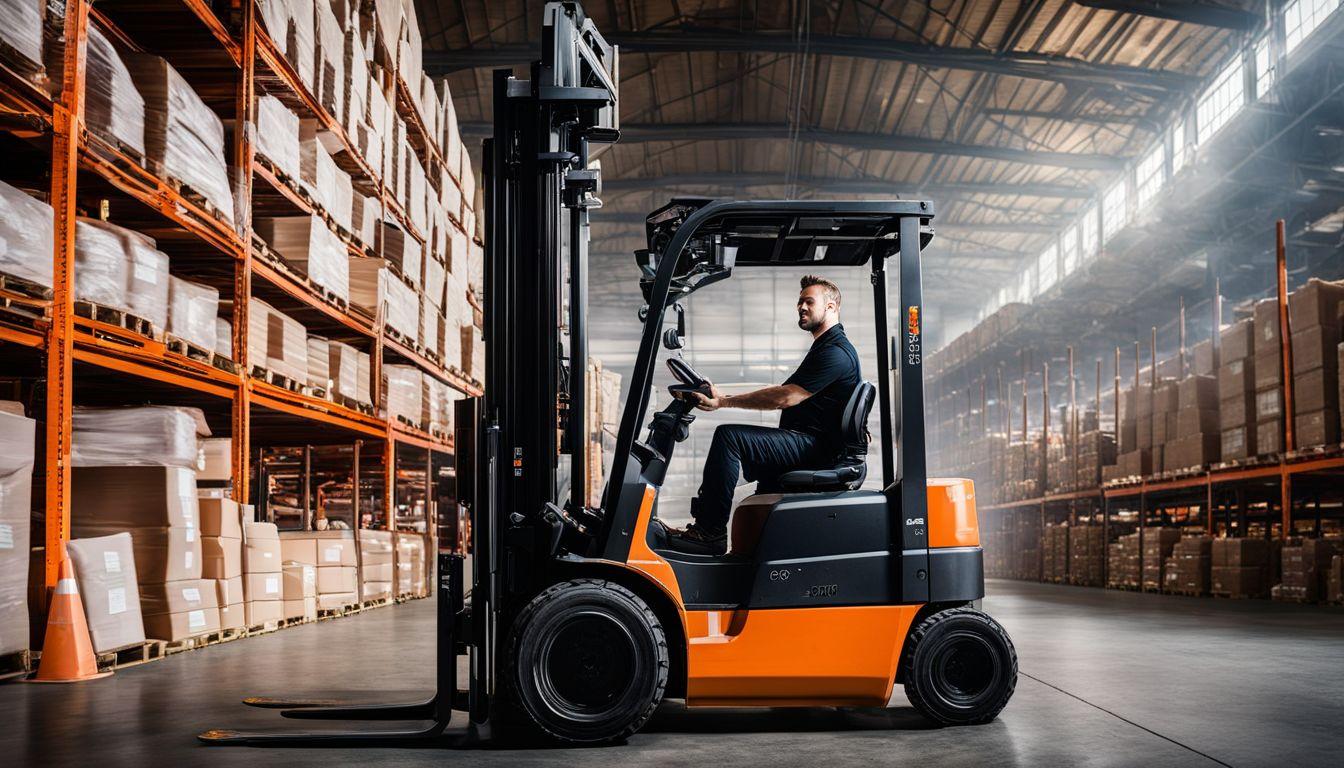
Before using a forklift, it is crucial to conduct a daily safety inspection. This includes visual pre-operation checks and operational inspections to ensure the forklift is in proper working condition.
Visual Pre-operation Inspection Checklists
Conducting a visual pre-operation inspection is mandatory for ensuring the safety and functionality of a forklift. These thorough checklists help operators identify any potential hazards or malfunctions before starting the machine.
- Check the operator compartment to ensure it is clean, with no loose bolts or damaged controls.
- Inspect the seat belt and parking brake to confirm they are functioning correctly and will hold the vehicle in place when engaged.
- Look over the mast and ensure its integrity; there should be no cracks, deformities, or hydraulic leaks.
- Examine forks, including the top clip retaining pin and heel, for any signs of wear, bending, or cracking that could lead to failures during use.
- Verify that load backrest extension is properly secured and capable of supporting a load without risk of shifting or collapse.
- Review both headlights and warning lights to make sure they are operational for visibility in dimly lit areas.
- Scan wheels and tires for damage like cuts or bulges that could impair safe operation of the lift truck.
- Test all gauges in the dashboard to confirm accurate readings that will guide safe operations throughout usage.
- Evaluate liquid levels such as coolant, engine oil, brake fluid, and if applicable, electrolyte levels in batteries; replenish as required following guidelines.
- Assess all belts and hoses under the hood for signs of wear or damage; replace parts showing excessive deterioration.
- Ensure battery restraints are secure to prevent movement that could disrupt electrical connections during operation.
- Confirm that safety decals and nameplates are clearly visible with legible operating instructions for driver reference.
Operational Inspection Checklist
Before a forklift takes on the day’s tasks, a thorough operational inspection is key. This process ensures each component functions correctly and safely.
- Start the forklift engine; listen for unusual noises that could signal malfunctions or needed repairs.
- Test the brake pedal to make sure it feels firm and brings the vehicle to a stop smoothly without any pulling to either side.
- Check that the steering mechanism operates easily and doesn’t stick, making sure it keeps the forklift on a steady course without any drift.
- Operate the lift control to raise and lower forks, ensuring smooth movement without delays or jerks.
- Inspect safety devices like lights, horns, and flashing beacons to confirm they are functional and visible from all directions.
- Examine the condition of seatbelts and other protective equipment; they must be in good shape to keep operators secure during use.
- Verify that all gauges are working correctly — fuel, battery charge, temperature, oil pressure — since these provide vital information about forklift health.
- Use tilt controls to move the mast forward and backward; it should do so freely with no stiffness or resistance.
- Activate warning signals such as backup alarms and check their audibility in a typical warehouse environment.
- Conduct tests on hydraulic systems by raising the load to full height then lowering it slowly; look out for leaks or drops in pressure that indicate issues.
- Monitor exhaust emissions for excessive smoke or fumes which can not only harm health but also suggest combustion problems.
- Confirm that radiator fluid levels are within acceptable limits, preventing overheating during extended operations.
Specific Inspections for Different Types of Forklifts
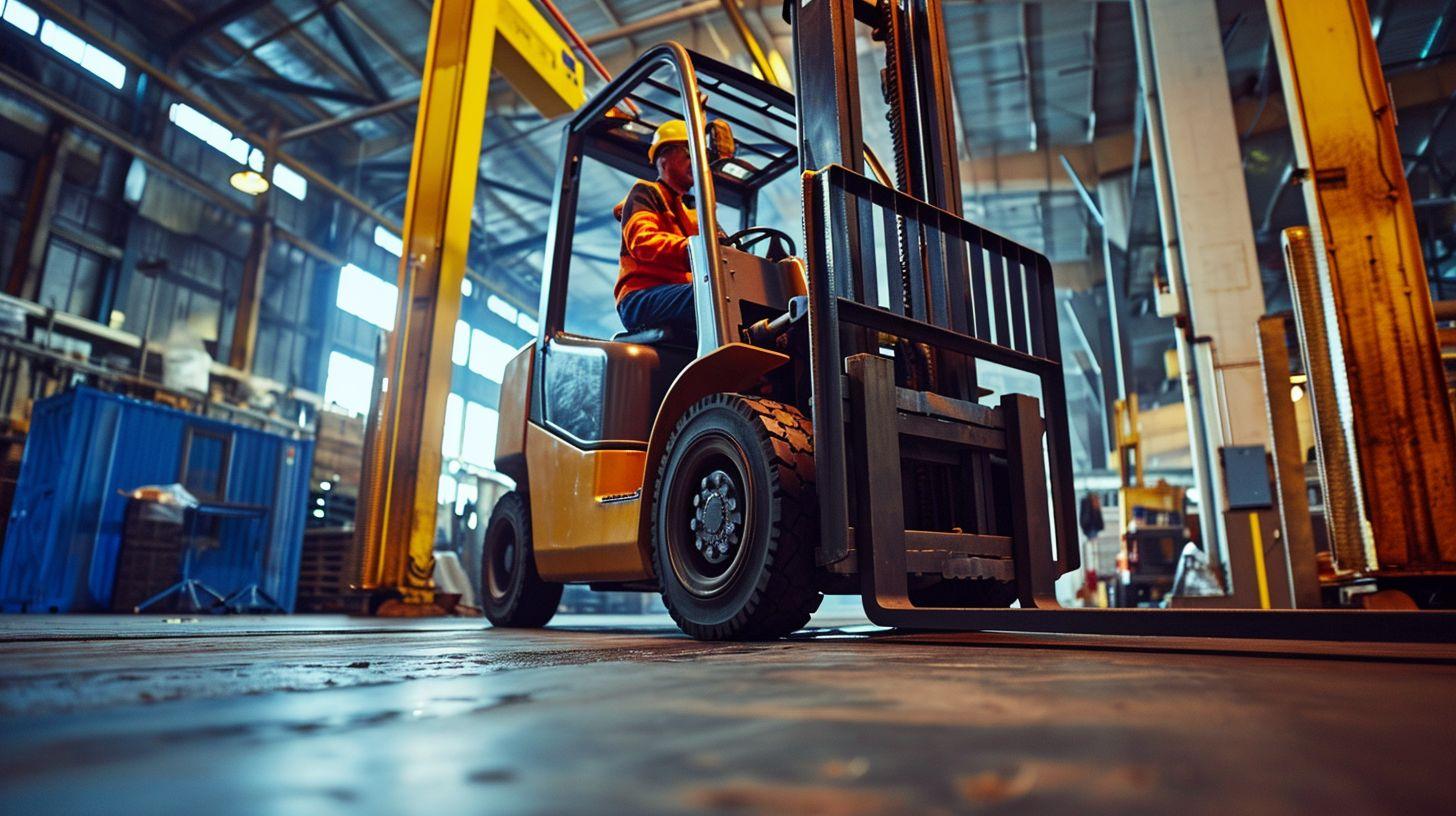
When it comes to conducting daily safety inspections, different types of forklifts require specific checks. For example, electric forklifts may need battery and charging system inspections, while internal combustion forklifts may require engine coolant and oil level checks.
Understanding the specific needs of each type of forklift is crucial in ensuring their safe operation.
Electric Forklifts
Electric forklifts demand a unique set of safety inspections before daily use. It’s essential to follow a comprehensive checklist to ensure they are operating safely.
- Start by inspecting the cables for any signs of wear or damage. Frayed or exposed wires can lead to electrical hazards.
- Check all connectors to make sure they are secure and free of corrosion, as poor connections can affect the forklift’s performance.
- Examine battery restraints to confirm they are in place and functioning properly. Batteries must be secured to avoid accidents during operation.
- Assess electrolyte levels in batteries, ensuring they are within recommended levels to maintain proper battery health and longevity.
- Make sure that the hood latch is firmly closed. An open latch can obstruct the operator’s view or lead to parts becoming dislodged.
Internal Combustion Forklifts
Before using an internal combustion forklift, it is crucial to conduct specific inspections to ensure its safe operation. Daily checks must include examining the engine oil, engine coolant, air filters, radiator, and hood latch for any signs of damage or leaks. It is also important to inspect the tires for proper inflation, wear, and tear.
Liquid Propane Forklifts
Liquid propane forklifts require specific inspections, including checking the tank mounting, pressure relief valve, connectors, hoses, tank condition, and proper fitting. These checks are vital to ensure safe operation and prevent accidents. Here are key components that need to be examined as part of the daily safety inspection:
- Tank Mounting: Verify that the tank is securely and properly mounted to the forklift frame.
- Pressure Relief Valve: Inspect the pressure relief valve to ensure it is in good working condition and free from blockages.
- Connectors and Hoses: Check all connectors and hoses for signs of wear, leaks, or damage.
- Tank Condition: Examine the overall condition of the propane tank for any signs of rust, corrosion, or other damage that may compromise its integrity.
- Proper Fitting: Ensure that the tank is properly fitted to the forklift with no loose connections or fittings.
Safety Considerations During Forklift Operation
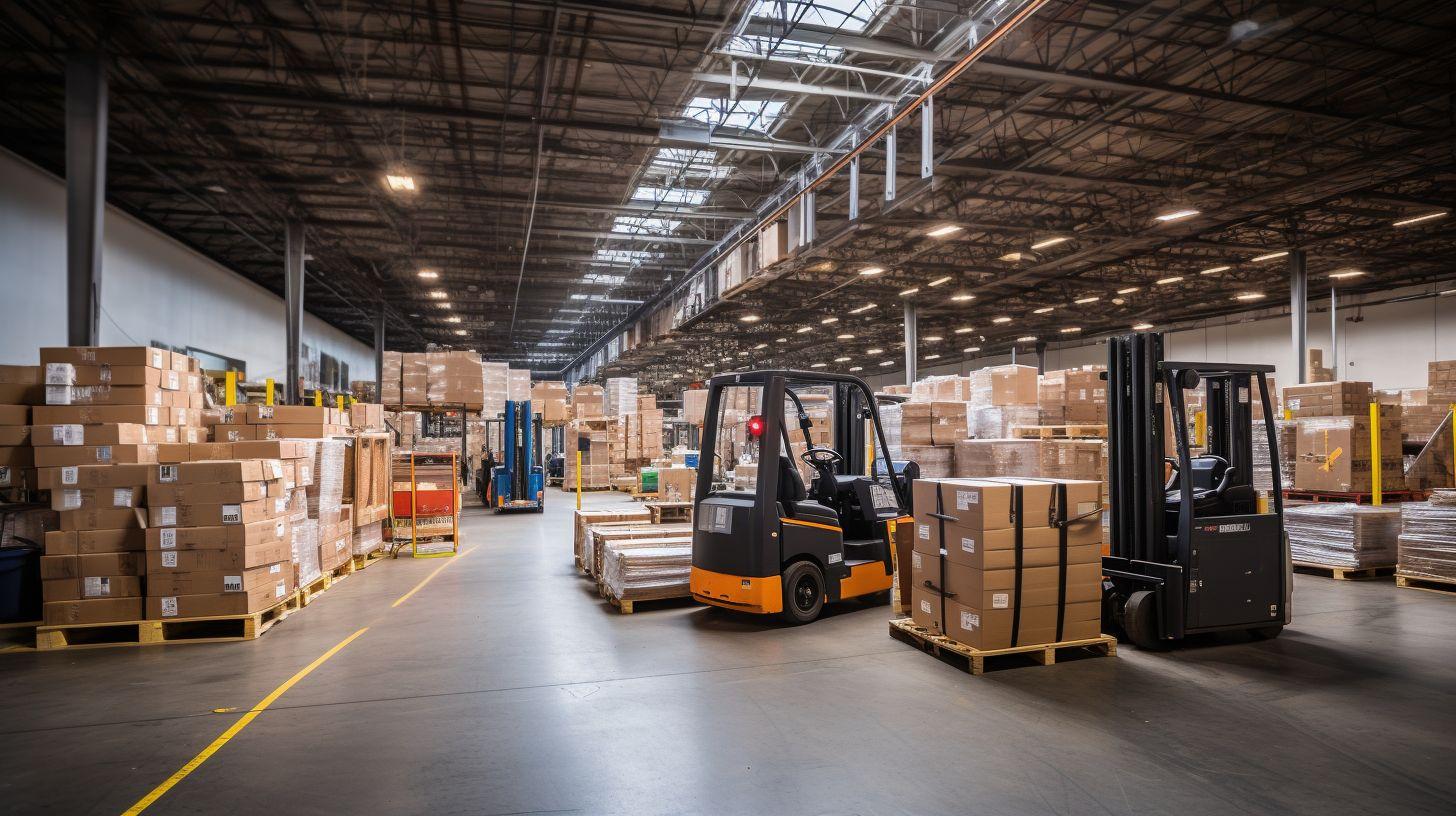
Ensure to always wear the seatbelt and keep all body parts within the confines of the forklift during operation. Operate at a safe speed, allowing ample time for braking and maneuvering.
Be vigilant of pedestrians and other equipment in the work area, using caution while turning and reversing. Avoid distractions that may affect your ability to operate the forklift safely, such as mobile phones or radios.
Regularly check that warning lights are functioning properly, indicating reverse gear or operational status. Keep an eye on hydraulic controls to ensure they are responsive and correctly manipulate loads.
Always observe load capacity limits and avoid overloading.
Inspect your surroundings before starting any task to ensure adequate visibility from the operator compartment. Conduct thorough inspections of operating controls before use, ensuring their proper functionality.
Finally, report any malfunctions or safety concerns immediately.
Long-Term Forklift Truck Maintenance Checks
Long-term forklift truck maintenance is crucial to ensure the continued safety and efficiency of the equipment. This section will discuss the various maintenance checks needed at different intervals to keep forklifts in top working condition.
Minor Maintenance (250 hours)
Perform minor maintenance checks every 250 hours of forklift operation to ensure safe and efficient functioning. This includes:
- Inspecting fluid levels to prevent potential leaks and ensure proper lubrication for the engine, transmission, hydraulic system, and coolant system.
- Checking for any leaks in the hydraulic system, oil seepage, fuel tank or lines, and coolant as per OSHA requirements to maintain a hazard-free environment.
- Assessing the condition of mast chains for any signs of wear or damage that may compromise lifting safety.
- Verifying tire conditions by inspecting for cuts, gouges, uneven wear patterns, or exposed cords to guarantee optimal traction and stability.
- Examining fork condition to identify any cracks, bends, or excessive wear on the forks that could affect load bearing capability.
- Ensuring the load backrest extension is secure and undamaged to provide protection against shifting loads during operation.
- Checking finger guards for damage to prevent potential harm from moving parts during operation.
- Verifying the presence and legibility of safety decals for visibility instructions and warnings required by OSHA guidelines.
- Confirming the availability of the operator’s manual in the designated storage area within reach of operators at all times.
- Testing functional safety devices such as lights, alarms, seat belts, horns,
Intermediate Maintenance (500 hours)
At 500 hours of forklift usage, the following maintenance tasks must be carried out to ensure optimal performance and safety:
- Inspect the engine cooling system, including hoses, belts, and radiator for any signs of wear or leaks. Replace or repair as necessary.
- Check the ignition timing and adjust if required to maintain efficient engine operation and fuel consumption.
- Examine the oil filter and replace it to prevent contaminants from circulating through the engine, which can lead to damage.
- Test the accelerator function to ensure smooth and responsive operation during use.
- Verify the condition of all valves and replace any that show signs of wear or malfunction to maintain proper fuel combustion.
- Inspect roll-over protection structures (ROPS) for any damage or deformation, ensuring they are capable of providing adequate protection in case of a tip-over incident.
Major Maintenance (2,000 hours)
At 2,000 hours of use, forklifts require major maintenance tasks to ensure their continued safe and efficient operation. These tasks include:
- Replacing coolant to maintain proper engine temperature regulation and prevent overheating.
- Changing the fuel strainer and water separator to ensure clean fuel supply and prevent engine damage.
- Replacing distribution belt and gasket seal to maintain proper engine performance and prevent leaks.
- Cleaning or replacing the interior ventilation filter for optimal air quality within the operator’s cabin.
- Replacing wheel bearing grease to minimize friction and wear on wheel bearings, ensuring smooth operation.
- Replacing transmission filter and oil to maintain proper lubrication and smooth gear shifting.
- Changing hydraulic oil to ensure proper hydraulic system function and prevent equipment failure.
- Changing brake fluid for reliable braking performance and overall safety.
How to Operate a Forklift Safely
Obtain OSHA-approved certification and understand the forklift type. Keep the forklift clean, be aware of the work area, and follow safety precautions to ensure safe operation.
Obtain OSHA-Approved Certification
To operate a forklift, it is essential to obtain OSHA-approved certification. This certification ensures compliance with safety standards and reduces the risk of accidents. Forklift operators must undergo training and complete daily inspections as mandated by OSHA to obtain this crucial certification.
Regular inspections help prevent potential hazards, maintain a safe work environment, and reduce the likelihood of injuries or damage.
Completing forklift inspection reports is necessary for obtaining OSHA-approved certification. These reports document that the pre-operational tasks and safety checks have been completed in accordance with OSHA regulations.
Understand the Forklift Type
Different types of forklifts, such as electric pallet jacks and internal combustion forklifts, have specific operational requirements. It’s important to obtain OSHA-approved certification and understand the particular type of forklift being operated before use.
This ensures that proper safety measures are taken into account and that the equipment is used in accordance with its individual specifications.
Knowing the specifics of a particular forklift type is crucial for maintaining a safe work environment. Keeping them clean, being aware of the work area, and understanding speed limits are all essential components of safe operation.
Keep the Forklifts Clean
Regular cleaning of forklifts is crucial to ensure safe and efficient operation. Clean the forklift daily to remove any debris, dirt, or other potential hazards. Use a soft brush or compressed air to clean out dust and debris from the engine compartment, radiator, and brakes.
Inspect the forklift for any signs of fluid leaks and promptly address any spills or drips. Regularly check the tires for wear and tear, as well as removing any buildup of mud or other substances that could affect traction.
Maintaining cleanliness extends beyond just the exterior; regularly inspect and clean filters, such as air filters, to prevent clogging which can impact engine performance. A clean forklift not only promotes safety but also helps identify potential maintenance issues before they become more significant problems.
Be Aware of the Work Area
After ensuring the forklifts are clean, it is crucial to be aware of the work area before operating them. Daily inspections should involve checking for any potential hazards or obstacles in the vicinity.
Additionally, operators must keep an eye out for changes in the work area, such as new obstacles or hazardous materials. It’s important to be mindful of other workers and pedestrians in the area to ensure their safety while operating a forklift.
Being aware of the clearance height and width of the work area is essential to avoid collisions or accidents. Furthermore, operators should pay attention to the type of surface they are operating on as different surfaces may require different techniques for safe forklift operation.
Conclusion
Performing a thorough daily forklift safety check is crucial to ensure safe operation. The responsibility for completing the inspection lies with the operator, in line with OSHA standards.
Specific inspections are required for various types of forklifts, such as electric, internal combustion, and liquid propane models. Employers must provide comprehensive checklists to comply with safety guidelines and reduce liability risks.
Regular inspections not only prevent accidents but also facilitate predictive maintenance and cost savings.
FAQs
1. Why do I need to inspect a forklift every day?
Daily forklift inspections are required to ensure safety and health at the workplace, as guided by OSHA (Occupational Safety and Health Administration).
2. What steps should I follow when doing a pre-use forklift check?
Before using a forklift, check the operator manual, look over all parts of the equipment including tires and controls, and make sure there’s no damage or hazards.
3. Can daily checks on a forklift help prevent accidents?
Yes! Daily checks can identify potential issues early which helps in preventing personal injury and unsafe working conditions around construction equipment like forklifts.
4. Should I wear any special gear when operating a forklift?
Always wear personal protective equipment as suggested in the health and safety guidelines to protect yourself from flames or other dangers while using a forklift.
5. What kind of maintenance should be performed regularly on a forklift?
Regular preventive maintenance, such as checking fluids like liquefied petroleum gas (LPG) levels or hydraulic pumps, is key to keeping your machine running smoothly.
6. Where can I find information about whistleblower protections if I report an unsafe situation with my company’s equipment?
Information about whistleblower protections under U.S Department of Labor’s Occupational Safety and Health Administration regulations can often be found within your workplace hazard communication resources or directly from OSHA.